Inventory Management and Its Impact on Financial Statements - Henderson Edition
2024.8.19
Inventory management involves controlling when, what and how much inventory can be ordered, stored and used for a company. It is an important management function involving controlling the inventory quantities of raw materials, components and products held in finished goods. Inventory management plays a major role in a business financial health. It is the function strongly influencing financial statements, either positively or negatively.
Importance of Inventory Management
Proper inventory management helps businesses to keep the right balance between having too many or too few products in stock to meet the demand of their customers. The balance of stock is important because it has several benefits such as:
Cost control: Carrying too much inventory ties up capital (eg, money) which could be put to work elsewhere in the business (eg, marketing, growing the business, paying your staff), increases storage costs, and exposes the company to the risks of obsolescence and recalls. Carrying too little inventory can result in stockouts, lost sales and very unhappy customers.
Benefits of Bookkeeping
Cash flow Optimisation: By effectively and continuously monitoring stock levels, inventory management helps improve cash flow, since businesses don’t have to spend as much money on unsold stock. This means the cash is available for other purposes, such as paying bills, or for earning higher returns by investing in company growth.
Operational Efficiency: By making inventory management more efficient, the business can reduce the amount of time and effort needed to handle stock, which in turn enables orders to be fulfilled more rapidly, improving customer satisfaction.
Types of Inventory
In preparing for a career in the grocery industry, it is vital to be aware of the various types of inventory. These can be organized into the following main categories.
Raw Materials: Also known as ‘inputs’, these are the basic materials going into the manufacturing of a goods. Here, the focus is on managing a company’s raw materials, which should be done properly to make sure production doesn’t stop.
Work-in-Progress (WIP): These are half-finished products currently being produced. This category of inventory is used to keep a track of production and identify bottlenecks.
Finished goods: These are finished items ready for sale. Maintaining a finished goods inventory means the appropriate products are available to meet demand at the required time without overstocking.
Maintenance, Repair, or Operations: Materials needed for the production process but not part of the final product. For example, you need some cleaning supplies, tools, and parts to maintain your machines. By controlling MRO items management, you can minimize downtime and continue to produce products proficiently.
Inventory Management Techniques
Several techniques can help businesses manage their inventory effectively:
Just-In-Time (JIT): Stock level is held at a minimum as supplies arrive only to the point where they are needed for use in production or sale. This reduces storage costs and waste, but requires accurate forecasting of demand and reliable suppliers.
Economic Order Quantity (EOQ): EOQ is a formula for calculating the order quantity maximizing total inventory costs (ordering, storing, etc) and helps a business to strike a balance between much stock.
ABC analysis: It categorizes inventory into three groups – A, B and C – depending on their respective value and importance. ‘A’ are high-value products with low frequency in sale; ‘B’ are moderate-value products with a moderate frequency in sales; ‘C’ are low-value products with a high frequency in sales. The focus on ‘A’ items helps the business know where it should focus its efforts and resources on its most critical inventory.
Safety Stock: a small quantity of extra inventory which is kept to prevent demand surges or supply chain issues (eg, a delivery being delayed). Stock-outs are to be avoided at all costs because it reduces customer satisfaction.
Impact on Financial Statements
Inventory management plays a critical role in a company’s financial statements. The statements directly related to inventory management are balance sheet, income statement, and cash flow statement.
Balance Sheet:
Inventory Valuation: Inventory is classified as a current asset, and valuation of inventory is very important because it will influence total assets and the total net worth of the company.
Turnover Ratio: A measure of how many times a company’s inventory is sold and replaced during a given period; a high turnover ratio is a sign of efficient inventory management, while a low ratio may indicate overstocking or sluggish inventory.
Income Statement:
Cost of goods sold (COGS): COGS measures the direct cost of goods sold by a company. By having tight control over inventory, COGS can be reported and used to calculate gross profit and net income more accurately.
Gross Profit Margin: The difference between sales and COGS expressed as a percentage. Good inventory management can contribute to business efficiency, both in reducing production costs for the same output and in minimizing waste.
Cash Flow Statement:
Inventory Management: Managing your company’s inventory efficiently not only increases your operating cash flow but also improves your company liquidity by reducing costs. Since you have less cash tied up in your stock, you are able to cover your short-term obligations in a timelier manner.
Cash Conversion Cycle (CCC): This is the period of time for a company to convert money invested in inventory to cash. Reduction of CCC comes from an effective inventory control thus a certain benefit is derived from a timely inventory turnover into sales and consequently to cash.
Challenges in Inventory Management
Despite its importance, inventory management comes with several challenges:
Demand Forecasting: Knowing what your customers are going to buy, especially strategically important products, is quite challenging to predict, in particular in industries with seasonality or trends changing rapidly (think lumber). Overestimating your demand can lead to lost sales and stealing market share, while underestimating it can lead to stock-outs and overstocks.
Supply chain disruption: Unforeseen incidents (eg, natural disasters, strike action, supplier issues) can disrupt the supply chain, while the availability of materials may have unexpected impacts on inventory levels. Businesses need contingency plans in order to manage these risks.
Inventory Accuracy: Keeping better inventory records is important because it helps you get the most out of your inventory management efforts. Inventory inaccuracies can result in stockouts, overstocking, and ultimately higher costs. This is where audits come in handy and where barcode scanners and the use of inventory management software help.
Obsolescence: Inventory obsolescence is when a company’s products and/or parts become outdated, are replaced or fall out of fashion, such as VHS tapes. This is a pervasive problem in markets which see rapid advances in technology, such as cell phones, or changing demands by consumers, such as clothing fashions. Companies have to regularly review their inventory and be alert to obsolescence issues.
Best Practices for Effective Inventory Management
Here are some best practices which can be adopted to overcome any challenges and improve inventory management:
Use Technology: Inventory software can be used to automate various physical and inventory processes, improving accuracy and speed. For example, real-time tracking and automated reorder points can be set up to match inventory records, ordering and receiving functionality can integrate with accounting systems, and reporting functionality can be used to analyze inventory performance.
Regular audits: Just like the weekly audit of your bank statements at home, regular inventory audits help to keep things on track and catch discrepancies as they arise. For example, cycle counting, where a portion of inventory is counted on a scheduled basis, can help keep things accurate while maintaining the pace of operations.
Supplier relationships: Relationships with suppliers are a classic area for improvement because they facilitate communication and enhance reliability. Collaborating with them on demand forecasting and inventory planning can result in reduced lead times and less supply chain disruption.
Continuous improvement: The company should regularly review and analyze processes related to inventory management to identify ways to improve. – Openness to new techniques and technologies: The company should be open to changing existing techniques and technologies to adopt better ones.
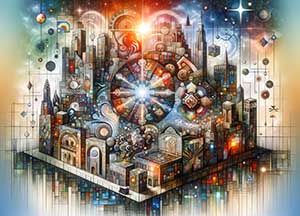
We List Only the Best
We bring the right peo1st Henderson Guide is not a list of every business. Our website highlights only the best businesses / places / events are featured within these pages. This makes Henderson even more magical for residents and visitors alike. ple together to challenge established thinking and drive transform in 2020
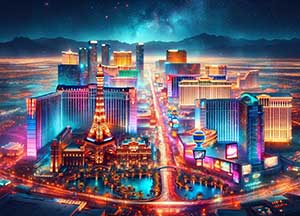
Advertise Your Company
You can be seen by a high quality audience when you place an advertisement on 1st Henderson Guide. Not all companies are accepted… Call 702-445-9488 to be have your company seen by affluent buyers. You will be amazed how with the low price.
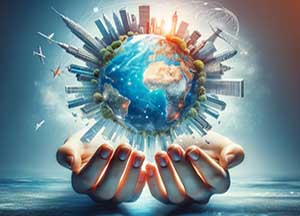
1st City Guide Expansion
1stCityGuide.com is the parent company of 225+ city guides worldwide. We are expanding and looking for Licensee partners to work together and provide a quality income when sharing the secrets of great cities around the world with visitors and residents alike. Call 702-210-4201 to discuss pricing and city guide availabilities.